Járműplatform, a láthatatlan védőkeret
A közúti járművek fejlődéstörténete során műszaki szempontból radikális változásokon ment keresztül a járművek alváza, felépítménye – mind anyagfelhasználás, mind pedig a teherviselő elemek kialakítását illetően.
Az alábbi cikkben megfigyelhetjük az platform konstrukciók múltját, valamint képet kapunk a jelenlegi helyzetről, és bemutatunk egy jelenleg is használatban lévő anyagot.
Mi az az alváz – és mi az a platform?
Konstrukciós szempontból kétféle építési módszert különböztetünk meg – és ezek átmeneteit.
Az alapvető különbség minden esetben az, hogy hol találhatók a teherviselő elemek.
Az alvázkeret a kocsitest tartószerkezete, hordozó része. Feladata, hogy a felépítményt, a futóművet és a hajtóművet egyetlen egységgé fogja össze, megadva az egész járműnek a megfelelő merevséget, s fölvegye a szállítmányból adódó terhelést. Lényeges pont, hogy mindezt a karosszéria segítsége nélkül teszi meg.

Az alvázkeretek legelterjedtebb formája sokáig a létra-alváz volt; amely két hossztartóból és kereszttartókból állt. Ma már azonban igen változatos alakú alvázakat gyártanak, melyek nagy része azért ma is visszavezethető az eredeti megoldáshoz.
Eleinte a tartókat még fából, ill. acéllemezzel erősített fából készítették, később hengerelt árut (L,U,I rudat vagy csövet) használtak.
Ma már általában acéllemezből sajtolják a tartókat, mivel így lehetőség van az alaknak, ill. a keresztmetszetnek hossz mentén való változtatására.
A hossztartók általában U-szelvényűek, de zárt négyszög keresztmetszetű tartók is előfordulnak. A kereszttartók lehetnek még kalapszelvényűek vagy egyszerű L-szelvényűek is. A zárt keresztmetszetű tartók lényegesen nagyobb csavarómerevséget adnak, de hátrányuk, hogy gyártásuk bonyolultabb, és más tartóelemek, tartozékok, szerelvények hozzáerősítése is körülményesebb, mint a nyitott keresztmetszetűek esetén.
Itt azonban nem állt meg a fejlődés. Lássuk a fő irányzatokat.
A differenciál építésmód („a” ábra) legnagyobb előnye, hogy a karosszéria kialakításakor a konstruktőr viszonylag nagy szabadságot élvez. A karosszéria csak néhány pontban és viszonylag rugalmasan van az alvázra erősítve, arról könnyen levehető. A főbb méret- és súlyhatárokon belül lényegében bármilyen karosszéria elképzelhető. Ugyanarra az alvázra autóbusz vagy teherautó felépítmény tervezhető, azok tetszés szerint módosíthatók, fejleszthetők. Lényegében ezt nevezzük a köznyelvben klasszikus „alvázas” építésnek.
Az átmeneti építésmód legegyszerűbb fajtája a kapcsolt építésmód, fejlettebb formája a padlóvázas felépítmény. Ebben az esetben a felépítmény közvetlenül és mereven rá van erősítve (csavarozva, hegesztve) az alvázkeretre („b” ábra). Ilyenkor tehát az alvázkeret valamivel gyengébbre méretezhető, mert a karosszéria vázszerkezete a terhelés egy részét magára veszi. Ezt az építésmódot főleg autóbuszokon és személygépkocsikon alkalmazzák. A differenciál építésmóddal szemben az integrál építésmód már nem ad teljes szabadságot az alvázkeret vagy felépítmény kialakítására, nem lehet tetszőleges alvázra tetszőleges felépítményt feltenni, viszont sülycsökkenést lehet elérni, mert a felépítményhez nem kell külön padlóvázat készíteni. Hátránya, hogy a padló alatti tér nem használható jól ki az autóbuszokon.
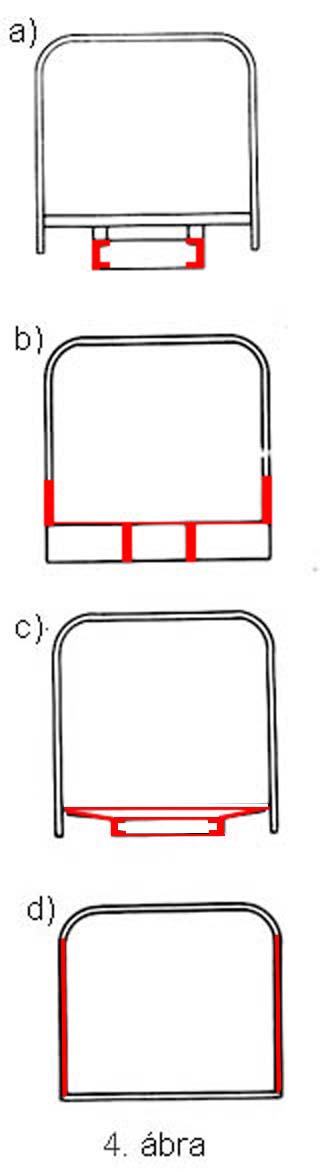
A padlóvázas szerkezeten („c” ábra) már elmarad a klasszikus formájú alvázkeret, de az alépítménynek még mindig kiemelt szerepe van a teherviselésben. Különösen személygépkocsikon alkalmazzák, amikor a felépítményt a nyitható tető miatt nem lehet megterhelni, vagy egyáltalán nincs teherbíró felépítmény (pI. nyitott sportkocsin). A padlóvázas szerkezet előnye, hogy a padlószint és a kocsi alsó széle közötti tér meglehetősen magas, különösen autóbuszokon, s így könnyű tartóelemekből nagy merevségű alépítmény-szerkezet alakítható ki. Balesetbiztonság szempontjából kedvezőbb, mint az alvázas megoldás.
Az önhordó kocsiszekrény („d” ábra) a könnyű-szerkezetekre való törekvés eredménye, aminek a célja az volt, hogy minden beépített keresztmetszetet vegyünk igénybe teherviselésre is, éspedig mindegyiket egyformán, a legnagyobb mértékig kihasználva. Ez azt jelenti, hogy ha pl. szükség van lemezborításra a külső hatások (eső, szél, hideg stb.) ellen, akkor az a lemez vegyen részt a kocsitest merevségének, ill. szilárdságának a. kialakításában is. Ez a törekvés a vékonyfalú szerkezetekhez, a lemezszerkezetekhez, ill. a héjszerkezetekhez vezetett.
Belátható tehát, hogy az idő előrehaladtával fokozatosan tértünk át az önhordó karosszériára – ez persze nem jelenti azt, hogy személygépkocsiknál ne találnánk alvázas kialakítást. Bizonyos terepjárók, nagyobb pickupok még ma is alvázas felépítménnyel kerülnek gyártásba.
Az önhordó karosszériák ún. platformokon nyugszanak, melyek ugyan részei a karosszériának, a gyártók mégis törekednek arra, hogy többféle karosszériát építhessenek fel egyazon platformra. Ennek természetesen költségcsökkentési okai vannak.
Anyagfelhasználás
Miközben a személygépkocsiknak egyre könnyebbé kellett válnia a károsanyag emisszió folyamatosan szigorodó szabályozása következtében, egyre ellenállóbbá is kellett tenni őket a potenciális közúti balesetekkel szemben.
Ezen ellentmondás feloldásához az anyagtudományt kellett segítségül hívni.
A járműipar számos szegletében általános probléma a minél könnyebb és minél erősebb szerkezeti anyagok fellelése.
A mai autókban számos helyen fellelhető az alumínium és annak ötvözetei, sőt, bizonyos esetekben szinte az egész járműváz abból készül – azonban az acélok szakítószilárdságát még a legerősebb alumínium-ötvözetek is igen nehezen érik el. Jellemzően ezeket az anyagokat kombinált módon használják fel az építés során. Ezek összekapcsolásához pedig sokszor speciális kötési technikákat alkalmaznak (vágószegecs, ragasztás, hegesztés). Ezek az ún. multimaterial koncepciók.
Az anyagtudományról ebben a témában is rengeteg áttörést említhetnénk – most az acélok közül választottunk ki egyet.
Egészen az utóbbi évekig tartotta magát az a megállapítás, hogy bármilyen acélról is legyen szó, az nem lehet egyszerre rugalmas és nagy szakítószilárdságú. Amikor nagyszilárdságú acélt akartunk előállítani, az mindig merev, törékeny volt (lásd: MART acélok), a kiváló rugalmasságú acélok pedig soha nem tudtak igazán nagy szilárdsági jellemzőkkel előrukkolni (pl. kis széntartalmú acélok, IF).
A legújabb fejlesztésű acélok esetében sikerült mégis olyan hőkezelési és technológiai megoldásokat találni, amelynek eredményeként mind a szilárdsági, mind pedig a képlékenységi mutatók egyaránt nagy értékűek. Ezek az acélfajták a DP (Dual Phase: kettős fázisú), TRIP (Transformation-Induced Plasticity: fázisátalakulással kiváltott képlékenységgel rendelkező) és a TWIP (Twinning-Induced Plasticity: ikresedéssel előidézett képlékenységgel rendelkező) acélok.
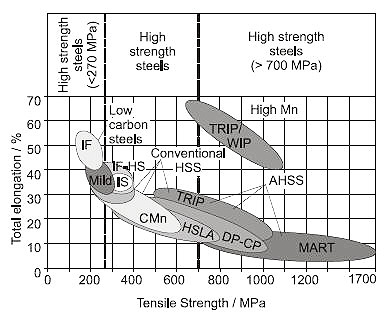
Ezek közül a jelen és a közeljövő egyik meghatározó anyagát, a TWIP-et mutatjuk be.
A TWIP acélok tekintélyes mennyiségű (17-24%) mangán ötvöző tartalmuk miatt szobahőmérsékleten is tisztán ausztenites szerkezetűek. Nagymértékű deformációra képesek, amely részben az ausztenites szerkezet miatt, részben pedig deformáció hatására a kristályszerkezetben az ún. ikerkristályok megjelenése miatt adódik.
Az ikerkristályok határfelületeit is figyelembe véve a TWIP acélok szövetszerkezete rendkívül finomszemcséssé, esetenként már nanoszemcséssé is alakulhat, ahol a jellemző szemcseméretek 100 nanométernél kisebbek, és az ilyen szerkezet a szilárdság szempontjából a legkedvezőbb szövetszerkezet.
A szakítószilárdság a TWIP acéloknál az 1000 MPa értéket is meghaladhatja, mellyel már bőven a használható tartományon belül helyezkedik el az anyag az iparág szempontjából.
A mangán ötvöző mellett a TWIP acélok még 3%-nyi alumínium és szilícium ötvözőt is tartalmaznak. A tekintélyes mennyiségű ötvözők miatt a TWIP acélok fajsúlya is jelentősen kisebb, mint a hagyományos acéloké, amely újabb járulékos haszon a járművek tömegcsökkentése szempontjából.
A TWIP acélok előnyei kiválóan hasznosíthatók a járműkarosszériákban. Az ütközéstesztek ezen anyagok esetében a legsikeresebbek, ezen kívül az alkalmazásukkal a tömegcsökkentés is számottevő. Ez az anyagcsalád jó példa a humán jólét és biztonság számára kifejlesztett új anyagokra.